Hier
der obligatorische Aufriss nach
dem Schwerpunktberechnungsprogramm von Dietrich Meissner..
Dieses ist wie ebenso die
Ruderberechnung, von seiner HP herunter
ladbar: http://home.germany.net/100-173822/schwerp.htm
hier die aufgerissene
rechte Flächenhälfte
und deren Rippenanordnung
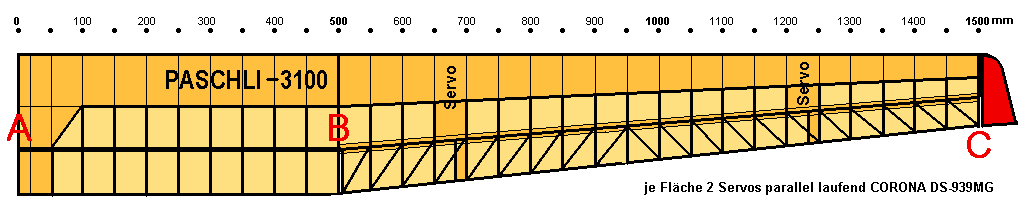
Bedingt durch 1m lange Querruder ist es sinnvoll diese
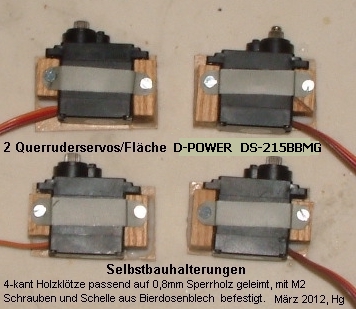
mit 2 gleichlaufenden
Servos an zu steueern.
Da kaum 20m/s = 72Km/h Anströmgeschwindigkeit mit diesem
Flooter
erreicht werden, ist die Summe beider Servomomente auch im Extremfall
völlig ausreichend.
Herstellerdaten:
Abmessungen: 22,5 x 11,5 x 24,6 mm
Gewicht: 12,5g
Betriebsspannung: 4,8V / 6V
Stellkraft: 2,5 Kg/cm /2,7 Kg/cm
Geschwindigkeit: 0,14 sec/60(4,8) /0,12 sec/60(6)
hier
die Rippenschablonen
aus 2mm ALU hart
hier
die Rippenblöcke
aus 3mm Balsa
in der Mitte 6 Rippen aus 2mm Flugzeugsperrholz, 3 links - 3 rechts und
die Trennung für 2 Flächenhälften in der Mitte
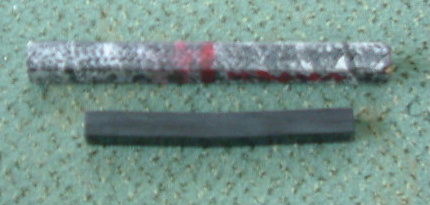
Als Flächenverbinder habe ich eine Steckverbindung 12 x 13
einer Ellipse-2 verwendet, die mir die passende V-Form erbringt.
Das Steckrohr wurde nittels 0,6mm Flugzeugsperrholz, was mit einem
Kohleschlauch und Glasband umwickelt in Verbindung mit EPOXY,
hergestellt.
hier die Holmgurte aus
Balsa/Kohle/Balsa alle 1m lang
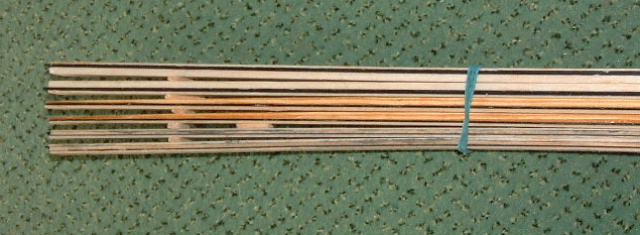
1 und
2 = Holmgurte Mitte
bis zum Querrudern = 2 x11mm Carbon, oben/außen 0,8Balsa,
unten/innen 2,5mm Balsa, alles mit Harz verklebt.
3 und 4 = Holmgurte
-Außenflächen oben = 1,5 x 8mm Carbon, oben/außen 0,8
Balsa,
unten/innen 3mm Kiefer, alles mit Harz verklebt.
5 und 6 = Holmgurte -
Außenflächen unten = 1 x 11mm Carbon, oben/außen
0,8mm
Balsa, unten/innen 2,5mm Balsa, alles mit Harz verklebt.
Die Balsabeklebung der Kohlegute
ermöglicht eine bessere und einfachere Verklebung mit
Weißleim,
der eine Verbindungen des Ober- mit dem Untergurt und
Balsaklötzen eine Holmverbindung erbringt.
==============================================================
Bisherige Planung und
Bearbeitung, im Mai 2010,
demnächst gehts weiter!
Jetzt gehts weiter, im März 2012.
Der Rippenabstand wurde zur besseren
Profilhaltigkeit und Torsionsfestigkeit der Bespannung auf maximal 40mm
gehalten.
Zumal etwa 5 Rippen mehr nur ein Mehrgewicht von 5...7g erbringen,
Flächen im Aufbau
Die Torsionsbeplankung (Profilnase) ist mit 3mm Balsa mittelhart
beplankt. Wobei zur besseren Profilierung beim Aufbringen
der Beplankung die Oberseite leicht angefeuchtet und mit Stecknadeln
fixiert wird, bis der Weißleim angezogen hat.
Selbstverständlich und letztendlich, damit kein
Propellerflügel entsteht, wird der Aufbau auf einem exakt
geraden Baubrett gemacht.
Wie es in allen Baubeschreibungen wie z. B. von Franz Perseke und
Werner Thies empfohlen wird, wurde.
Aus diesen Empfehlungen ist es sinnvoll den eigenen Möglichkeiten
und Gepflogenheiten die besten einem liegenden heraus zu suchen
und oder daraus eigene Methoden zu entwickeln.
Dieses erbringt meistens eine sehr große Zeitersparnis, wobei ein
Eigenbaumodell dann oft um einiges schneller zu bauen ist, als manch
ein
käuflicher Bausatz!
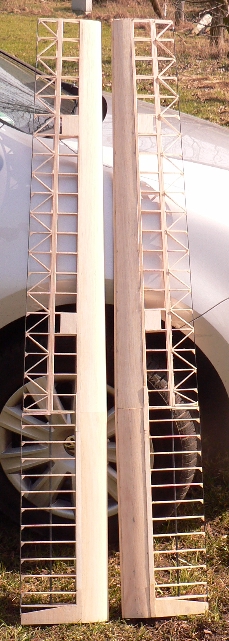
endlich Märzensonne und
raus
auf die Wiese zum Schleifen. Beide Flächenhälften
rechts noch
nicht und links nach dem ersten Formschliff.

Bild links:
Herstellung
aus Kohleroovings in einer aus Balsaleisten hergestellten Form.
Bild rechts: Das V-Leitwerk fertig verschliffen, noch nicht geteilt und
abgetrennten Fläpsen.
Im Ganzen geschieht die Herstellung und erst anschließend
erfolgten die Trennungen der Ruder. Die Teilung besteht noch bevor.
Anschießend
wurde alles mit einem
Spannlackanstrich zur besseren Verbindung des Bespannmaterials
(Polyestergewebe) versehen.
Ein mit Balsaleisten ummanteltes 4mm Kohlerohr dient als Holm.
Die Rippen und Gitterstege wurden mit Sekundenkleber an dem Holm, sowie
der Nasen- und Endleiste verklebt.
Die Profilierung wurde während des Schleifens mit Schleifbrettern
hergestellt
Als Endleisten der Flächen, Querruder wie dem Leitwerk, wurden
1,5mm Kohlestäbe verwendet, was sich mehrfach bewährt hat,
einfach
anzubringen ist, aber sehr stabil ist, auch nach dem Schleifen bei der
Profilierung.
Da die wechselweise Verstrebung an
den Querrudern sich sehr gut bewährt hat, habe ich dieses auch
für die Leitwerksfläpse verwendet,
deshalb sind die Abweichung, auch
der Optik wegen, von
den vorab Plänen gemacht worden, die ich nicht noch einmal
Zeichnen,
oder abändern wollte.
Besitzt aber die gleiche
statische Festigkeit, wie Torsionsfestigkeit. Ist mehr aus
Geschmacksache geschehen
.
im
März 2012, Hg
===================================================================
Hier nun Aufnahmen vor und nach
der
Bespannung (eine
Woche vor Ostern 2012)
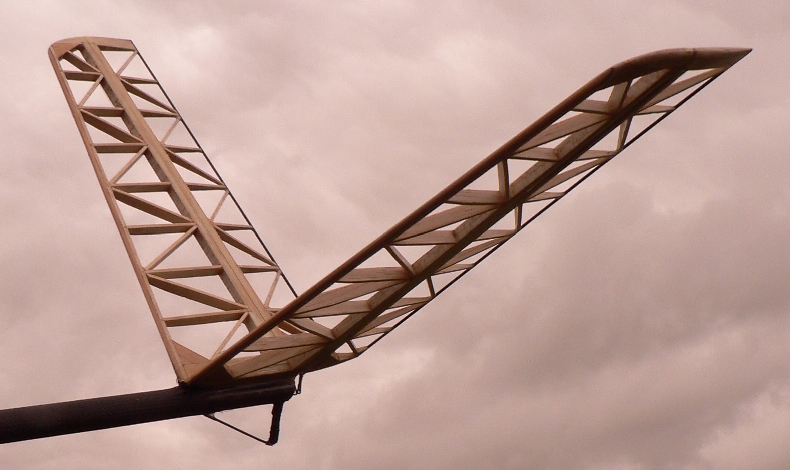
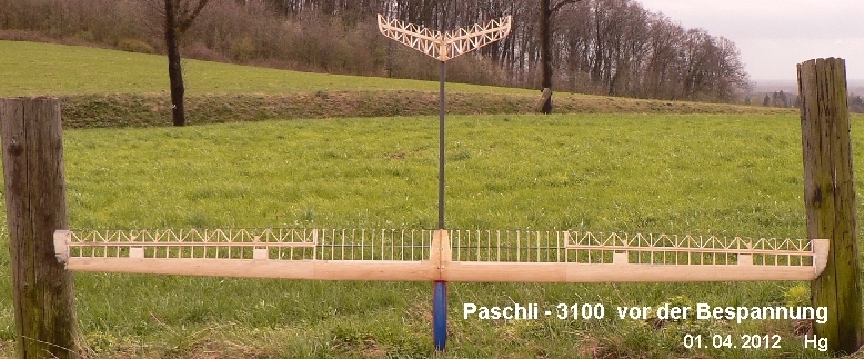
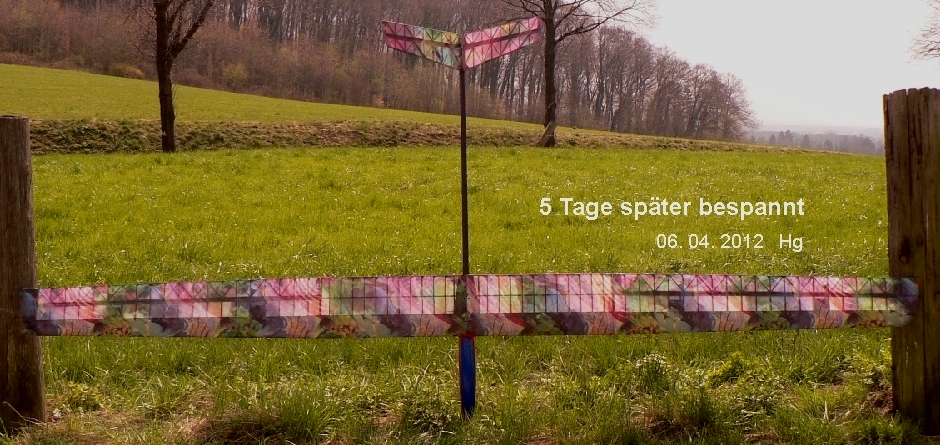
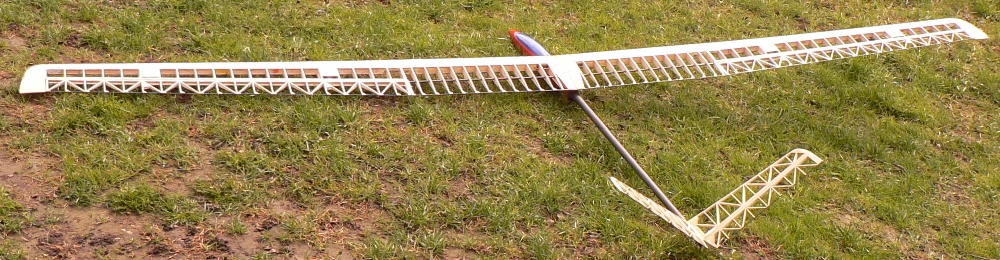
Im
Rohbau und voll ausgerüstet, liegt das Gewicht exakt bei
1453g bei
61dm²
Flächeninhalt, liegt die Flächenbelastung bei 23,82g/dm²
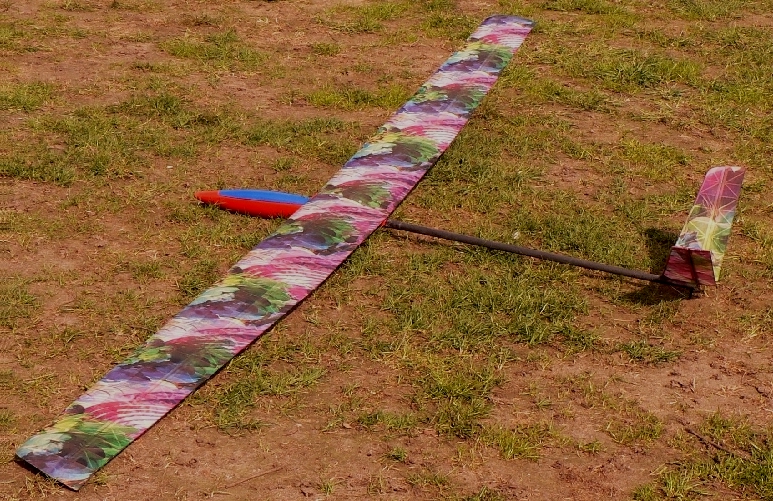
Das Fluggewicht beträgt 1550g, was einer Flächenbelastung =
25,4g/dm²
ist. Nach FAI incl. Leitwerk = 23,45g/dm².
Nachträglich (vor der Ausrichtung und Einklebung des Rohres mit
dem LW), noch ein zusätzlicher Kohleschlauch mit
Epoxydharz (etwa 22g) afgebracht,
der eine sehr große
Steifheit des langen LW-Trägers brachte.
Damit entfielen auf die Bespannung nur etwa ganze 80g. Die nach einigen
Tagen den letzten noch nötige Spannlackanstrich bei einem
hoffentlich etwas
wärmeren Wetter stattfinden wird,
da Spannlack möglichst bei einer Temperatur gleich besser
über 20°C aufgebracht werden sollte.
Die gesamte, effektive Bauzeit für das Modell betrug etwa 50h
ganz. Obwohl eine
Windenfestigkeit dazu bei einem Gewicht
geringer als 25g/dm²
Flächenbelastung beträgt
und dies alles ohne großen Maschinenaufwand.
Auch hatte ich für den Bau nicht die Möglichkeiten wie ich
sie früher einmal hatte, dieses alles mit einem Maschinenpark
einer Holz-
und Metallwerkstatt her zu stellen,
wo ich sogar mir die passenden Leisten u. s. w. Schneiden konnte.
So habe ich
die meisten Arbeiten auf einem kleinen Baubrett und z. T.
auf dem obligatorischen Küchentisch gemacht.
Man sieht, dass auch dieses geht, wenn man sich nicht vor ein wenig
Arbeit abschrecken lässt.
Die Bespannung der V-Leitwerkshälften und
Flächenhälften, habe ich jeweils in einem Stück
Chiffongewebe ohne Stückelung aufgebracht.
Hierbei wurden auch die später sehr leichtgängigen, aber
festen
Scharniere für die Ruder, mit diesem einem
Stück Chiffon (Polyestergewebe) gemacht.
Für weniger geübte Modellbauer von Bespannungen mit
Spannlack, empfiehlt sich das
einfachere, in mehreren Stücken Aufbringen der Bespannung, wie sie
von z. B.
von
Werner Thies und andere dies beschrieben hat.
siehe
auch
hier: 2besp.htm
Die Bespannung wird im Drehpunkt zusammen
geführt!
.
5 Handstarts an einer kleinen,
kaum tragenden Wiese mit sehr geringen Gefälle, verliefen
sehr positiv und erwartungsvoll.
Der bisherige optimale Schwerpunkt
liegt nach der Annäherungsmethode letztendlich bei 85mm hinter der
Nasenleiste.
Bedingt durch die relatief großen Querruder und dem 10%igem HLW
zur Fläche, sind nur geringe Ausschläge erforderlich. die
wegen eines geringproduzierten Widerstand ich als positiv
betrachte.
Wie bei meinem Paschli - 2300 werden die Querruder zum Höhenabbau
und zur Landung mit einer Tiefenzugabe nach oben
gestellt, wodurch zur
Abbremsung ein großer Widerstand erforderlich ist und die
Größe der Querruder ebenfalls positiv sind.
Effektive Bauzeit (nur geschätzt,
da ich kein Baubuch geführt habe) etwa 45 ... 55h
im
April 2012, Hg
====================================================================================
Es ist mir zu
schade dieses Modell nur als Segler ohne Antrieb zu fliegen.
Deshalb habe ich mich entschlossen für die Flächen einen
separaten Rumpf mit Elektroausrüstung
und einem eigenen V-Leitwerk zu bauen, sodass mir bei einem Rumpftausch
ein
2. Modell zu Verfügung steht.

Bild
1
Bild
2
Bild
1 1 = meine vor über 15-Jahren gebaute
Seglerform.
2 = daraus
der mit gekürzte und mit Sturz versehenen Nase, passend für
einen 45mm Spinner ausgelegt.
Das Laminat besteht aus Glasgewebe und leicht rot
eingefärbten Epox-Harz, sodass nur eine dünne Lackierung
ausreicht und ein Kratzer es rot
bleibt.
3 = die
zum Rumpf passende Haube. Mit schwarz eingefärbten Epox-Harz
und Glasgewebe. Keine Kohle für für
einen guten 2,4GHz-Empfang.
Bild 2 4 =
Leitwerkträger über einer Angelrute aus Epoxydharz,
einem Aramid- und einem Kohle- Schlauch hergestellt, der
über einer passenden Angelrute mit einer
Teflon beschichteten Backfolie zur besseren Trennung, laminiert wurde.
5 =
Schaumstoffabstandhalter die das im Leitwerkträger eingeschobene,
gelagerte Bowdenzugrohr fixiert.
6 = 3mm Bowdenzugrohr.
7 =
2 Stück 0,8mm Stahldrähte für die V-Leitwerkanlenkungen.
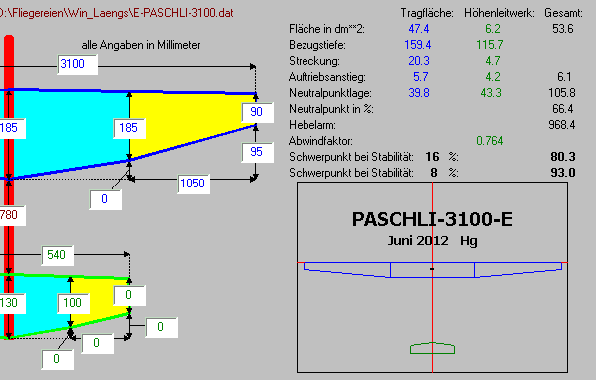
bedingt durch das erhöhte Gewicht im Nasenbereich, konnte
ein größerer Hebelarm für das VLW gewählt werden,
was der Längsstabilität für ein stressfreies
Thermikmodell zu gute kommt.
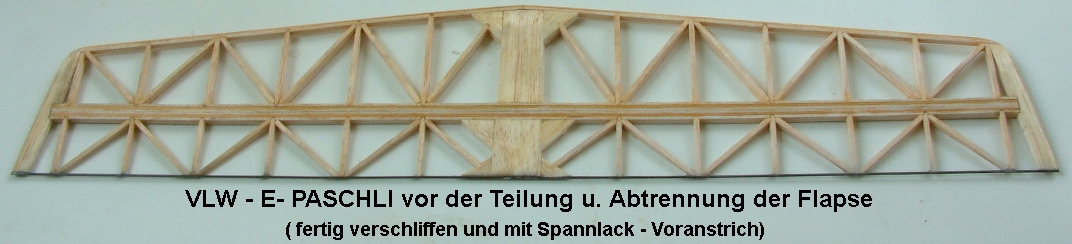
Nasenleiste = Kiefer/Balsa, Holme =
Balsa/Kiefer/Balsa, Endleiste = 1,5mm Kohlerundstab
auf 0,8mm geschliffen, Rippen + Stege = 3mm,
Spannwete gestreckt =
700mm,
42 Gramm
und hier mit dem Kohle-V-Verbinder
fertig zum Anbau an den
LW-Träger.
Die Fläpse/Ruder werden wie gehabt mit den bereits beschriebenen
Bespannmaterial als Scharnier verbunden.
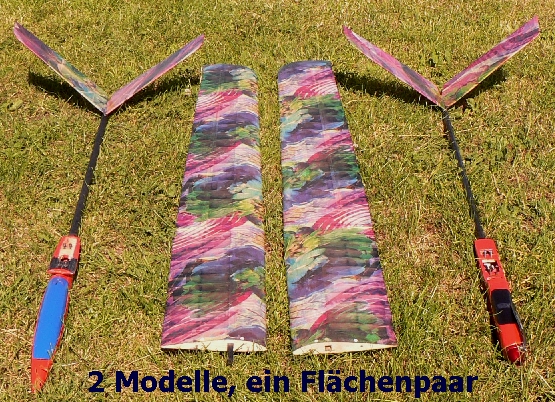
==========================================
nach einem schweren Crash, hatte der
Flächenverbinder einen Haarriss,
Da mir eine etwas größere V-Form der Fläche für
ein noch engeres Kreisen in sehr engen und schwachen
Thermikschläuchen mir für besser erschien, habe ich durch den
weniger gute Gelegenheit,
mir aus einem Carbon-Flachprofil 12 x 2mm, einen
Flächenverbinder von 5,5° mit Harz zusammengeklebt.
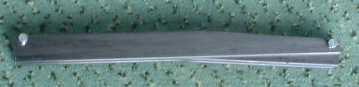
Bild Mitte: Die
einzelnen Teile habe ich habe ich in einer mit etwas Waschpulver
im Wasser und mit einem 350er Nassschleifpapier zur besseren
Verklebung, angeschliffen.
Bild Links und Rechts: Die
6 Einzelteile mit Hilfe der 2mm Bohrungen und Schrauben
für die Klebung vorbereitet.
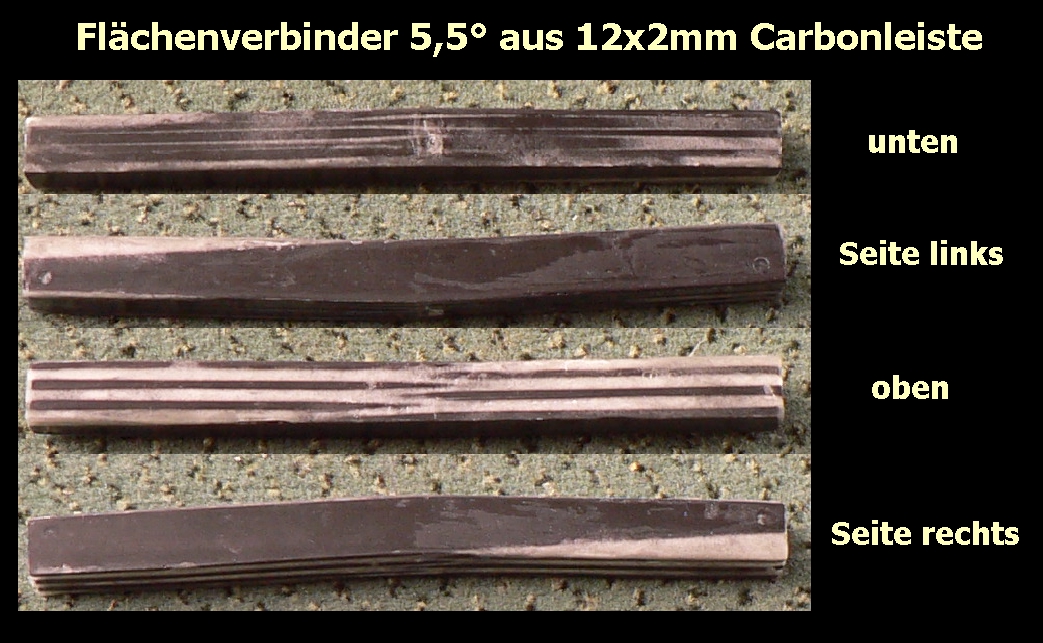
Durch die Lammellierung der aus Harz getemperten Carbonleisten ist
eine sehr große Bruchfestigkeit gegeben.
Die nach den Enden sich veringernde Höhe der wechselweise
verharzten Teile, sind keineswegs eine Schwächung.
da die zu haltenden Zug- und Druckkräfte dort bis auf 0 (Null)
zurück gehen!
Die Lücken durch
die keilförmigen Ausschnitte sind mit einem Gemisch aus
Mikroballons und Harz ausgefüllt.
im September 2012, Hg
ZURÜCK